The Good for Texas Tour: Supply Chains
By David Green, Shannon Halbrook, Lisa Minton and Edda Pleitez
Global supply chains are the arteries of the highly connected and interdependent world trade system. They create value, contribute to lower consumer costs, and increase economic efficiencies.
In particular, supply chains facilitate the movement of intermediate goods — parts and components of final goods. This inter-industry trade helps reduce production costs and is a key feature of advanced manufacturing processes.
Supply Chain Risks and Resilience
The benefits of global supply chains are intertwined with risks. The COVID-19 pandemic painfully revealed some of those weaknesses, but even before the pandemic, industry experts were exploring ways to address them.
Risks
Efficient, “just in time” manufacturing requires readily available intermediate goods and reliable shipping. Global industries are exposed to trade disputes and shipping backlogs.
Regional operations can be vulnerable to weather events or other local disasters. Diseases or health crises also can strike at any time, and cyberattacks are another growing threat.
Resilience
Balancing efficiency with resilience can help mitigate certain risks. Many businesses are rediscovering the value in reshoring (bringing some operations back to the U.S.), holding extra inventory “just in case” and adding redundancy across regions.
Advancements in technology can make supply chains more agile and adaptable to changes in availability or shipping conditions.
Greater use of artificial intelligence and sensor-equipped cargo infrastructure can help businesses closely monitor their operations, quickly spot disruptions and reroute supply chains as needed.
Furthermore, large companies that fortified their supply chains during the pandemic are preparing to sell extra cargo space as a service to other businesses.
Texas Supply Chains and the Comptroller’s Tour
With its 19.4 percent share of U.S. exports, Texas’s economy greatly depends on international trade and stable supply chains. State exports largely have recovered from the pandemic and have increased more than 10 percent from 2019.
Leading the way is a surge in oil, gas, and petrochemical exports to China and other countries, up 41 percent since 2019. With especially robust trade in intermediate goods, Mexico remains our state’s largest export destination.
Texas business leaders are reporting much stronger demand for goods and services this year, but supply chain issues remain a concern.
This fall, as part of his ongoing Good for Texas series of statewide tours, Comptroller Glenn Hegar visited several Texas businesses with strong trade relations and supply chains that exemplify the risks and resilience of their respective industries. He also visited a Texas port of entry that serves more than 150 manufacturing plants in Mexico.
“As the nation’s top state for international trade and the ninth largest economy in the world,” Hegar stated, “limiting supply chain disruptions is critical to the Texas economy.”
.
Tour Stop: Semiconductors — Texas Instruments (TI)
At the onset of the pandemic, semiconductor supply was curtailed by factory shutdowns in Asia. Meanwhile, the need for chips rose faster than expected, driven by sales of high-tech products used in remote work and school environments and followed by a surging demand by automobile makers.
In May 2021, a typical wait time for chip orders was 18 weeks, affecting nearly 170 industries. Chip production is lengthy and highly complex — taking up to six months for more advanced units — so shortages are expected to last well into 2022. Moreover, the U.S. accounts for only 12 percent of global chip manufacturing, which limits its capacity to ease the shortage.
A global semiconductor company, TI manufactures, tests, and sells analog and embedded processing chips that are key components for a variety of end-market products.
TI is currently expanding its Texas presence by building a new 300-mm wafer fabrication facility in Richardson as part of the company’s long-term capacity planning.
The facility should be ready to support production in the second half of 2022, increasing domestic production and the U.S. share of global production.
EXHIBIT 1: SEMICONDUCTOR MANUFACTURING IN TEXAS AND U.S., 2020
Source: U.S. Census Bureau, USA Trade OnlineTour Stop: Automobiles — General Motors (GM)
Tour Stop: Automobiles — General Motors (GM)
Motor vehicle parts represented the bulk — $8.3 billion or 71 percent — of the state’s automobile-related exports. That compares with a nearly 40 percent share nationwide, reflecting the importance of those products to Texas. More than 80 percent of Texas auto parts exports went to Mexico in 2020 (Exhibit 2).
EXHIBIT 2: MOTOR VEHICLE PARTS, EXPORTS TO MEXICO, 2020
Sources: U.S. Census Bureau, USA Trade Online; Texas Comptroller of Public Accounts analysis
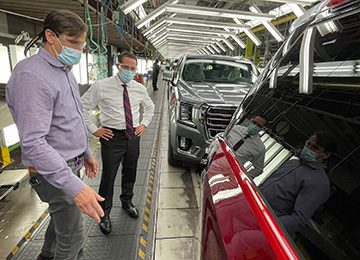
The automobile industry is particularly burdened by the semiconductor shortage.
In April 2021, chip shortages caused General Motors and Ford to pause production at several of their North American plants, affecting 10,000 GM workers.
Global automotive manufacturers were expected to produce 1.5 million to 5 million fewer cars than planned in 2021.
Texas is home to 13 GM facilities, employing more than 13,500 Texans who earn more than $1.3 billion in wages annually. The GM Arlington Assembly Plant builds 1,300 vehicles each day.
In response to supply chain challenges, automotive leaders have planned several strategies to build greater resilience in their supply chains, including dual sourcing of raw materials, increasing inventory of critical products, reshoring, regionalizing supply chains, and investing in digital technologies to improve supply chain visibility.
Tour Stop: Chemical Manufacturing — Dow Chemical
Wages in the industry average $113,372 annually, with more than 83,500 jobs statewide (primarily in Harris County).
Texas is the country’s top chemical producer and exporter. In 2020, chemicals were the third-largest export, with a value of about $40 billion, or 14.3 percent of the state’s total exports (Exhibit 3).
EXHIBIT 3: TEXAS’ CHEMICAL MANUFACTURING INDUSTRY ECONOMIC DATA
COUNTY | NUMBER OF EMPLOYEES, BASIC CHEMICAL | INDUSTRY CONCENTRATION, BASIC CHEMICAL | NUMBER OF EMPLOYEES, ALL CHEMICAL | INDUSTRY CONCENTRATION, ALL CHEMICAL |
---|---|---|---|---|
HARRIS | 12,129 | 5.13 | 24,832 | 1.82 |
BRAZORIA | 6,780 | 55.72 | 7,481 | 10.64 |
DALLAS | 1,383 | 0.79 | 6,901 | 0.68 |
TARRANT | 269 | 0.28 | 5,601 | 1.01 |
JEFFERSON | 2,286 | 19.16 | 3,747 | 5.44 |
Note: Data are for NAICS 325 (Chemical Manufacturing) and a subset, 3215 (Basic Chemical manufacturing).
Source: JobsEQ
Its products are found in many end-use items such as office supplies, pharmaceuticals, cleaning supplies, and food.
The chemical industry, made up largely of multinational businesses with suppliers of all sizes around the world, faces an array of local and global risks.
In a 2020 report, McKinsey & Company found the chemical supply chain to be most vulnerable to natural disasters, cyberattacks, and trade disputes. Industry insiders cite other risks as well, including chemical supply chains’ volatility, interdependence, and complex regulation.
Technology, digitization, and circularity — the recycling or reuse of chemical building blocks — are risk mitigation strategies that are being promoted by leaders in the industry to help circumvent supply chain issues.
Tour Stop: International Trade — Anzalduas International Bridge
Sources: U.S. Census Bureau, USA Trade Online; U.S. Bureau of Transportation ServicesEfficient border crossings facilitate the movement of people and goods between countries and are a key ingredient in the reliability of supply chains.
Trade between Texas and Mexico represents a significant contribution to the state economy, and the cross-border trade of intermediate goods is an integral part of many industries’ supply chains.
Likewise, Hidalgo County, with five of the state’s 11 border crossings, is an important center of trade (Exhibit 4).
The Anzalduas International Bridge connects Mission, in Hidalgo County, to Reynosa, Tamaulipas, Mexico. Reynosa is home to the manufacturing plants of more than 150 international companies, all situated within a 9-mile radius.
The bridge opened in 2010 and is owned and operated by the city of McAllen in partnership with the cities of Hidalgo and Mission.
Although electronics, machinery, and petroleum lead the way in trade value, the five Hidalgo County border crossings also are gateways for fresh produce into the U.S.
In 2020, $4.5 billion in fruits and vegetables were imported into Texas from Mexico for personal and commercial consumption.
Tour Stop: Food — Sysco
The Texas food supply chain links several industrial sectors: agriculture, manufacturing, warehousing, transportation, wholesale trade, and retail trade.
Sysco, a global company serving more than 650,000 customer locations worldwide, is a major distributor of food and kitchen products to Texas restaurants, hotels, schools, and more.
Overall, food supply chain-related industries contributed a total of $85.6 billion to the Texas GDP in 2020, representing 4.9 percent of the state’s total GDP. Of these industries, food services contributed the most, representing nearly 2 percent of the total.
The start of the COVID-19 pandemic led to grocery shortages; a year later, Winter Storm Uri along with the resulting power outages almost brought the state’s food supply chain to a halt.
Cyberattacks have been another threat to the complex food supply chain. In May 2021, Brazilian meat processor JBS USA fell victim to a ransomware attack, forcing production to shut down for a few days in its beef and pork processing plants around the world, including several facilities in Texas.
The attack was one of approximately 40 cyberattacks on food producers in the 12 months preceding the JBS incident.
Agriculture plays a major role in the state’s economy (Exhibit 5), and overall, the food-related sectors of these industries employ 1.5 million Texans and provide $40.5 billion in annual wages. Sysco alone employs more than 6,000 workers in Texas.
.
EXHIBIT 5: TEXAS AGRICULTURE
Tour Stop: Mineral Resources — USA Rare Earth LLC
Rare earth elements (rare earths) are a group of minerals crucial to the manufacture of products ranging from cell phones to wind turbines and fighter jets.
The United States relies almost exclusively on foreign sources of rare earths. In 2020, the United States imported 100 percent of its usable rare earth compounds and metals, with 80 percent coming from China.
A U.S. supply chain of rare earth metals is increasingly important to national security, but it must be built from the ground up. USA Rare Earth LLC, a critical mineral supply chain company, is building facilities to produce American-made rare earth magnets along with its joint venture partner, Texas Mineral Resources Corp.
In 2023, USA Rare Earth will begin mining 950 state-owned acres that are expected to yield more than 300,000 metric tons of rare earth oxides.
Combined with USA Rare Earth operations elsewhere, this domestic supply chain of rare earths would meet 17 percent of projected demand in the United States (Exhibit 6).
Tour Stop: Mineral Resources — USA Rare Earth LLC
Rare earth elements (rare earths) are a group of minerals crucial to the manufacture of products ranging from cell phones to wind turbines and fighter jets.
The United States relies almost exclusively on foreign sources of rare earths. In 2020, the United States imported 100 percent of its usable rare earth compounds and metals, with 80 percent coming from China.
A U.S. supply chain of rare earth metals is increasingly important to national security, but it must be built from the ground up. USA Rare Earth LLC, a critical mineral supply chain company, is building facilities to produce American-made rare earth magnets along with its joint venture partner, Texas Mineral Resources Corp.
In 2023, USA Rare Earth will begin mining 950 state-owned acres that are expected to yield more than 300,000 metric tons of rare earth oxides.
Combined with USA Rare Earth operations elsewhere, this domestic supply chain of rare earths would meet 17 percent of projected demand in the United States (Exhibit 6).
EXHIBIT 6: RARE EARTH PROJECTIONS FOR ROUND TOP DEPOSIT, SIERRA BLANCA, STARTING 2023
Source: USGS Earth Mapping Resource Initiative
Conclusion
The good news is that the difficult lessons learned during the past two years can help businesses strengthen their supply chains and better prepare for the future.
“I have seen an incredible amount of innovation during my tour of the state and in discussions with industry leaders committed to creating a stable, strong, and dynamic supply system,” Hegar says. FN